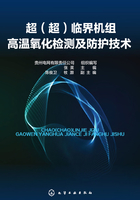
1.3 超(超)临界火电机组高温蒸汽氧化现状及危害
1.3.1 超(超)临界火电机组高温蒸汽氧化现状
金属与高温气体接触发生的氧化过程可以简单分为以下两阶段:第一阶段,氧气与金属表面直接接触,由于金属表面的氧分子在高温环境下分解成氧原子,而氧原子可以从金属中得到电子成为氧离子,故而与金属发生氧化反应,生成金属氧化物。随着氧化反应不断进行,反应物越来越多,最终形成覆盖于金属表面的氧化膜。第二阶段,则是一个电化学反应过程,氧化膜表面和空气中的气体接触,接触后氧分子分解成氧原子,被吸附的氧原子得到电子形成离子,氧离子从表面向内迁移,金属原子形成带电阳离子和电子从金属向氧化膜迁移并向外扩散,阴阳离子接触反应并形成金属氧化物。
1.3.1.1 国外高温氧化研究现状
发达国家的科研机构早在20世纪60年代初就对高温高压导致锅炉蒸汽侧氧化皮脱落这一现象进行了探索。1966年,美国Edison公司通过检测国内245台火力发电机组管道氧化情况发现,其中占总量85%的214台机组,出现了氧化皮大量剥落的现象,占总量54%的135台氧化皮剥落尤其严重,引发了科研工作者的广泛关注。
1978年,在总结包括CERL在内的多家科研机构试验研究成果的基础上,EPRI发表了总结性报告,对高温受热管蒸汽侧氧化膜的典型形貌、微观结构特征以及成分组成等进行了系统总结,并在对试验数据进行初步分析的基础上给出了一些当时使用较广泛的低Cr铁素体合金和奥氏体合金的蒸汽氧化动力学参数,为后续试验和理论研究打下了很好的基础。在此之后,世界范围内电力工业快速发展,发电机组蒸汽参数节节攀升,新型合金管材不断出现,受热管蒸汽侧氧化膜问题愈加复杂,迫切需要对合金高温蒸汽氧化动力学有更深入的理解。许多科研人员在这方面开展了大量试验研究工作,并通过对试验结果进行分析得到了T22、T91、TP347H、TP347HFG等电站高温受热管常用合金的蒸汽氧化动力学参数,即阿伦尼乌斯常数(arrhenius constant)和活化能(activationenergy)。
日本的超临界和超(超)临界锅炉大多使用TP347HFG、Super304,但仍有三个电厂超临界锅炉发生了氧化皮剥落问题,原因尚不清楚。德国有一个电厂超临界锅炉前几年也曾多次发生这类问题,管材牌号为TP347H,电厂为了减少这类问题的危害已经被迫降参数运行。澳大利亚某厂两台超临界机组自从2005年以来已经多次发生氧化皮大面积剥落堵塞问题,为此美国EPRI专家和我国西安热工研究院专家先后多次赴澳大利亚电厂进行检测和分析,但未提出妥善的解决方案。目前国外对于这一问题最常见的处理方法就是将容易出现氧化皮剥落问题的超临界或亚临界锅炉过热器和再热器部分甚至全部更换为抗氧化性能更好的高等级材料(如TP347HFG或Super304等)制成的过热器和再热器。
目前火电机组锅炉高温受热面常用合金主要有三类:以T22为代表的低Cr标准铁素体合金、以T91为代表的9Cr铁素体-马氏体合金以及以TP347H为代表的300系列奥氏体合金。试验发现,这三类合金蒸汽侧氧化膜的微观结构和形貌特征存在较大不同,是造成这三类合金受热管蒸汽侧氧化膜的失效形式存在差异的重要原因之一,就此开展了大量研究。
(1)低Cr标准铁素体合金的氧化
大量观测结果表明,低Cr标准铁素体合金蒸汽侧氧化膜一般呈双层结构,两层氧化膜的厚度相近;氧化膜的外层为Fe3O4层,由尺寸较大的柱状晶粒组成,多空隙,内层是Fe-Cr尖晶石层,晶粒尺寸相对较小且各向均匀;随着厚度的增加,在氧化膜的最外侧还会出现零星分布的Fe2O3。近来,有学者发现在T22合金受热管运行较长时间后,其蒸汽侧氧化膜可能会出现多个“双层结构”,在最初的双层氧化膜与基体之间会不断出现新的双层氧化膜,形貌和组成与最初的双层氧化膜相似。将该现象归因为锅炉停机过程造成蒸汽侧氧化膜发生贯穿式开裂,高温蒸汽随后沿着裂纹侵入管壁基体,从而形成新的双层氧化膜。然而,Wright I G和Dooley R B却发现,T22合金受热管蒸汽侧氧化膜中“双层结构”的数目与机组的停机次数存在很大差距。还有文献报道,在氧化膜较薄时,根据理论计算氧化膜不可能发生开裂,但通过光学显微观测,却仍在氧化膜中发现了多个“双层结构”,显然都与之前所给出的解释不太相符。到目前,出现这一现象的原因还没有完全研究清楚,需要进一步研究。
(2)9Cr铁素体-马氏体合金氧化
实验发现,在氧化初期,9Cr铁素体-马氏体合金蒸汽侧氧化膜主要由厚度相当的内、外两层氧化物组成,外层为Fe3O4层,内层为Fe-Cr尖晶石层。此外,在氧化膜与基体交界面处,还存在一些离散的富Cr氧化物。在外层氧化膜中存在较多的空隙,分析认为这是由氧空位坍塌造成的。在受热管运行一段时间后,内、外层氧化膜交界面处开始出现一些孔洞,使得外层氧化膜容易发生脱落。关于这些孔洞的成因,主要有两种观点:Sanchez L等基于T91合金在100%蒸汽中的氧化实验结果,推断认为是由Cr2OH、CrO3以及CrO2(OH)2等挥发造成的;而Wright I G和Dooley R B认为是由于Cr含量较高的Fe-Cr尖晶石层以及富Cr氧化物具有较强的保护性,有效抑制了铁离子向蒸汽侧的扩散,从而导致内、外层氧化膜交界面处出现大量Fe空位,随着氧化膜的生长,这些空位不断增多、变大、联合并最终演化为宏观孔洞。目前Wright I G和Dooley R B的观点得到了更广泛的认可,但还需要更多的试验研究来予以检验。随着氧化膜的进一步增厚,以及内、外层氧化膜交界面处孔洞的持续增多,基体金属离子向蒸汽侧的扩散迁移变得更加困难,这时外层氧化膜的最外侧会被进一步氧化为Fe2O3。
(3)300系列奥氏体合金的氧化
300系列奥氏体合金的蒸汽侧氧化膜整体上与铁素体合金氧化膜类似,也主要是双层结构,外层是Fe3O4层,内层是Fe-Cr尖晶石层,但在氧化膜/基体交界面处还存在一个层较薄的富Cr氧化物。该种合金蒸汽侧氧化膜的生长速率很低,同时外层氧化膜常含有较高比例的Fe2O3,有文献报道,将此归因于Fe-Cr尖晶石层以及内、外层氧化膜交界面处孔洞对基体金属元素向外层扩散的强烈抑制作用。另外,试验观测发现,TP347H等粗晶奥氏体合金的内层氧化膜形状极不规则,这是因为在金属晶粒交界面处相比于在晶粒表面更容易形成保护性富Cr氧化物,结果晶粒表面处氧化膜的生长速率远大于晶界处,从而形成了厚度极为不均的内层氧化膜。这一结构特征也使得内层氧化膜与基体有很强的结合力,因而一般不会在氧化膜/基体交界面处发生氧化膜脱落。对比结果显示,相比于粗晶奥氏体合金,TP347HFG等细晶奥氏体合金的氧化膜生长速率更慢。给出的解释是,细晶奥氏体合金相对较小的晶粒尺寸有助于基体Cr元素沿晶界迅速扩散至氧化膜/基体界面,使得在氧化初期便可形成连续分布的富Cr氧化物层,这有效抑制了氧化膜的进一步生长。
从以上研究可以看出,对不同类型合金的蒸汽侧氧化膜而言,其微观结构和形貌特征存在较大差异,这会对氧化膜的失效行为产生重要影响,因此在对这三类合金受热管的蒸汽侧氧化膜进行失效建模研究时,应区别对待,分别予以计算分析。
1.3.1.2 国内高温氧化研究现状
我国对金属氧化这一领域的研究起步较晚,相较大量超临界机组与超(超)临界机组的工程建设,理论研究层次还是没有跟上实际运行的脚步。不但理论水平还有待提高,工艺程度和技术要领也都掌握在国外发达国家手中,与此同时,我国高参数机组的运行管理理念还是同亚临界机组一样,没有特定的指导技术。所以,超临界锅炉因管壁氧化问题导致安全事故的现象时而发生,造成了巨大损失。目前,我国科研工作者对超(超)临界机组耗材的抗氧化能力做了如下研究。
国内学者张乃强和徐鸿等对T92、TP347HFG等合金在500℃和600℃,25MPa超临界水中进行了氧化时间最长达1000h的氧化试验,研究了溶解氧浓度对合金氧化动力学的影响,并绘制出了相应的氧化动力学曲线。
NF709钢是日本新日铁公司开发的一个新型奥氏体耐热钢,具有良好的高温抗氧化腐蚀能力和持久强度,可用于制造超(超)临界锅炉的过热器和再热器。王斌、刘正东等研究了N709钢的氧化性能,NF709钢在700℃蒸汽氧化作用下形成的氧化层可分为内、外两层。外层为疏松多孔的富铁氧化物Fe3O4,内层为致密的尖晶石结构的富铬氧化物(FeCr)3O4;有效阻止了铁和氧分别向外层和基体的扩散,使蒸汽氧化速率减慢,从而使得该钢具有良好的抗蒸汽腐蚀的能力。研究表明,N709钢有良好的抗蒸汽腐蚀能力,是锅炉过热器、再热器的优良材料。
黄兴德指出了因制作锅炉的材质不同,各自氧化皮晶粒特点也不同这一现象,并对各个特点进行了说明,同时也补充解释了氧化皮形成和剥落的因素。并且重点提出了要想阻止氧化皮生成不现实,应该进一步分析材料的特点和运行工况的特性,最终达到在实际运行时,预测、减轻以及及时处理氧化皮掉落所带来的负面危害,延长锅炉有效寿命。
徐敬军等研究了在650℃,Ar-H2O环境下,T91钢的高温氧化特性。通过对比T91分别在5%、7%、10%的Ar+H2O中氧化10h的氧化动力曲线,得出在5% Ar+H2O进行7min反应时,氧化增重呈抛物线规律,7%和10%环境下为分阶段的抛物线规律。同时蒸汽含量对氧化增速有着积极的作用。
边彩霞等针对电站锅炉蒸汽侧氧化膜在机组降负荷时可能会出现的剥落情况,利用有限元计算方法,通过对铁素体钢T91和奥氏体钢TP347H在这一时刻应力状态的模拟,指明二者都表现出径向压应力,应力随负荷的降低而表现出线性减小这一现象。铁素体钢在负荷降低的后期易发生脱落,而奥氏体钢在初期易发生脱落,电站应根据实际情况,控制停炉速度,保证锅炉安全。
李学东等对Super304钢的高温氧化情况进行了研究,发现在氧化初期,氧化膜表面呈现出沟渠状,氧化膜并不完整,黏附排列比较疏松,同时,表面形成颗粒状氧化物。随着氧化的进行,氧化膜变得致密,致密的氧化膜具有钝化作用,阻碍了离子的扩散与迁移,对试样起到了一定的保护作用。400℃条件下,Super304H钢试样表面氧化物为Fe3O4;在温度高于400℃时,试样表面氧化物的主要成分为Fe3O4和FeCr2O4,以及少量的Fe2O3,在高温蒸汽氧化初始阶段,高温蒸汽氧化速率由水蒸气分子在金属基体表面的吸附和分解速度决定。当Super304H钢表面形成了一层氧化膜后,氧化速率是由铁离子和氧离子通过内外氧化膜的传输速度决定的。
魏东斌等研究了TP347钢高温蒸汽氧化组织,发现在试验温度为800℃时,TP347H耐热钢的氧化动力学方程为y=4.7030t 0.4383,该方程符合氧化层长大的ΔW=kt的抛物线规律。TP347H钢的氧化皮由内、外两层组成,外层疏松,内层致密,外层达一定厚度时因裂纹产生而易于脱落,在氧化外层中,氧含量从外到内逐渐减少;Fe含量由内到外逐渐减少;在氧化层的内层中,Cr、Ni元素含量存在互补性的富集和贫化,即在同一位置,Cr高Ni低或Ni高Cr低,在氧化内层和基体界而处,Cr元素的富集程度可超过基体的正常值,在脱落的最外层氧化皮中Cr、Ni元素含量极低。
通过上述国内外研究对比来看,我国对金属高温氧化的研究与认识还刚起步,大多还处于摸索阶段,对于承温能力要求更高的再热器管材,尤其是奥氏体钢的研究更少,这对下一步发展高参数高负荷机组的前进有不小阻力。
1.3.2 超(超)临界火电机组高温蒸汽氧化危害
过热器与再热器管是工作环境最为恶劣的高温承压部件,其内壁承受高温高压蒸汽氧化,外壁承受高温烟气的腐蚀和煤粉颗粒的冲蚀。尤其是内壁的蒸汽高温氧化腐蚀一方面使管壁的有效壁厚减薄,应力增加,承载能力降低;另一方面使氧化形成的氧化皮达到一定厚度时会产生氧化皮脱落,并沉积于弯管处造成管子堵塞。此外剥落的氧化物颗粒会导致汽轮机前级叶片和喷嘴等的冲蚀以及汽门卡涩等。这一问题在现役超临界和超(超)临界机组中非常普遍,已成为困扰超(超)临界机组安全运行的一个突出问题。在实际火电机组运行中,锅炉受热面氧化皮剥落后会对机组安全运行产生以下主要影响。
(1)导致锅炉受热面超温爆管
超(超)临界锅炉受热面金属在高温高压环境中可以与蒸汽直接反应生成氧化皮,当氧化皮达到一定的厚度时就会发生剥落,带来多方面的问题和不良影响。
在中国,超(超)临界火电机组中主蒸汽的运行参数一般温度为540~600℃,压力为2~30MPa,再热器会因吸热量增长而比过热器所受温度高几十甚至上百摄氏度,所以锅炉再热器管道金属受热面承受的温度压力更为巨大,再热器管材便有着更苛刻的热强性、组织稳定性和抗氧化性。
近年来,工程上再热器管道事故多为材料的抗氧化性不足而引起的,即再热器材料在高参数工作环境下管道内壁氧化速率骤升以致产生氧化皮并且脱落,无法正常排除并堵塞在管道内部,尤其是在弯头或出口处,导致超温爆管。在全球范围内已经是影响锅炉管道失效的第二大原因,金属表面每形成0.2~0.5mm厚的氧化皮,就相当于形成1600~3600g/m2的结垢量。在机组启停炉阶段,由于锅炉管壁温度变化较大,氧化皮发生剥落的风险最大。如图1-2所示,在高速蒸汽的曳引下,剥落的氧化皮颗粒会随蒸汽一起流动,但仍一部分质量较大的氧化皮颗粒会在管道的弯头部位或焊缝位置处停滞堆积,堆积的横截面越大,发生爆管的概率就越大。某电厂亚临界锅炉末级过热器前段发生氧化皮堵塞爆管(材质TP304H),爆口形貌如图1-3(a)所示,为典型的厚唇形爆破,爆口两侧管子发生不同程度的胀粗,爆口处横截面有大量的微观裂纹,如图1-3(b)所示,爆口截面经金相组织观察,发现部分晶界发生滑移,晶界处存在较多的微裂纹和洞穴,符合超温特征。

图1-2 氧化皮在管道底部弯头或焊缝处堆积示意图

图1-3 氧化皮堵塞爆管
某电厂600MW超临界机组在升负荷准备进行168h满负荷试运时,连续多次发生垂直水冷壁管(材质15CrMoG)爆管泄漏,经内窥镜检查时发现,在垂直水冷壁入口90°弯头处堆积有大量的氧化皮并将弯头堵死,管子内壁及氧化皮情况如图1-4所示。

图1-4 垂直水冷壁入口弯头处氧化皮堆积导致的爆管
据文献报道,武汉某电厂的WGZ670/13.7-4型号的高压中间再热自然循环锅炉,在运行了20000h之后,高温过热器的58根管排,频频发生爆管事件,令机组无法正常运行,严重影响了电站的安全经济运行。冷态启动600MW机组,耗油速率180t/h,同时还要支付修复的材料费用和人工的费用,经济损失相当巨大。1000MW超(超)临界锅炉如发生故障,经济损失则会更大。
(2)固体颗粒会造成汽机喷嘴、阀杆和叶片的侵蚀损坏
从锅炉过热器或再热器剥落的氧化皮,很大一部分被蒸汽携带至汽机,经喷嘴加速后,获得较高的动能,撞击汽机喷嘴和动叶后,会使汽机高、中压转子前几级叶片受到损伤,一方面会降低汽轮机的级效率,另一方面也会降低叶片的强度,严重时会造成汽机断叶片。研究发现,固体颗粒侵蚀问题大多在机组投运数年后才开始出现。为了解决这一问题,国外把它作为重点问题组织进行研究,并在1974年的美国动力会议上发表了专论。在1981年的英国材料性能杂志上以及1983年的美国动力会议上发表了此专题的论文和一些解决措施的报道。1999年,美国EPRI还为给水加氧处理是否会引起过热器管氧化皮的剥落问题进行了研究,最后得出结论,认为不同的水工况对过热器氧化皮剥落没有什么影响。过热器氧化皮的剥落,主要是由于运行工况的条件,如超温和温度压力变化以及材料等方面因素所造成的。
2015年3月,位于北京市的某热电厂发生火灾,事故调查组调查技术报告表示,该事故是由于该厂2号机组汽轮机中处于干、湿蒸汽交替区的第20级叶轮轮缘在运行中突然断裂,断裂源于在长期运行中产生的微裂纹,直至裂纹扩展至剩余承载面积不足以承受叶片离心力的时候,汽轮机叶片发生断裂。本次事故直接经济损失为988.46万元,由于发电机组冷却使用的氢气与运行中的油发生爆燃,瞬间产生的“黑烟”和“蘑菇云”对环境造成了不可逆的影响。
(3)影响水汽品质,增加汽水中铁含量
被高速蒸汽带出锅炉过热器、再热器的氧化皮剥落物颗粒,在汽轮机内完成对叶片的撞击和冲蚀以后,颗粒本身会被破碎、变小、变细,并增加了一些叶片本身被冲蚀的产物进入凝汽器。这些颗粒中的90%粒径为5~50μm,可以随水汽自由移动到蒸汽所能到达的地方,成为热力设备最易结垢部位(水冷壁、高加水侧)沉积物的主要来源。
(4)造成锅炉受热面进一步超温
由于金属氧化皮的热导率低于金属母材的热导率,因此锅炉受热面内壁生成金属氧化皮后会造成导热热阻上升,从而造成管材的进一步超温。由此可见,锅炉氧化皮剥落不仅会引发锅炉爆管,对汽机主汽门及通流部分以及对水汽品质均会产生较大的影响。而防止氧化皮的剥落也是一个系统工程,需从机组运行方式、水汽品质控制及设备管理等方面进行综合考虑。