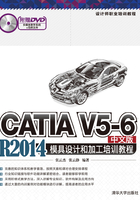
第1课 1课时 设计师职业知识——模具分型概述
本课首先介绍分型面设计的功能和选取原则。
1.注塑模向导模块分型面设计
所谓分型面,就是模具上用以取出塑件和浇注系统凝料的可分离的接触表面,也叫合模面。分型面的功能就是创建修剪型芯、型腔的分型片体。
注塑模向导模块提供了创建分型面的多种方式,创建分型面过程的最后一步为缝合曲面,可以手动创建片体。分型面的类型、形状及位置选择得是否恰当,设计得是否合理,在模具的结构设计中非常重要。它们不仅直接关系到模具结构的复杂程度,而且对制品的成型质量、生产操作等方面都有很大的影响,如图2-1所示就是一个产品的分型面。
图2-1 分型面
2.分型面选取原则
在选择分型面时,我们要遵循以下一些基本原则。
(1)分型面应选择在塑件外形的最大轮廓处。塑件外形的最大轮廓处,也就是通过该方向上的塑件的截面最大,否则塑件无法从型腔中脱出。如图2-2所示,在A截面能顺利脱模,而选在B截面则不能取出塑件。

图2-2 分型面放在尺寸最大处
(2)分型面的选择应有利于塑件成型后能顺利脱模。通常,分型面的选择应尽可能使塑件在开模后留在动模一侧,以便通过设置在动模内的推出机构将塑件推出模外;否则,若塑件留在定模,脱模会很困难。通常在定模内设置推出机构推出塑件,会使模具结构非常复杂。在图2-3所示的模具中,从分模面开模后,2的部分为模具的定模部分。模具的定模部分开模后固定不动。一般情况下,定模部分没有推出机构。从分模面开模后,1的部分为模具的动模部分。模具的动模部分在开模时由注射机的连杆机构带动模具的动模移动,打开模具。动模部分设有推出机构,由注射机上的液压系统推动模具上的推出机构使塑件从动模中推出模外,实现塑件自动脱模的过程。

图2-3 有利于脱模的分型面
实际模具中,因为动模有型芯,塑件成型后,会朝中心收缩,使得型芯上的开模力大于定模上型腔的开模力,塑件可以留在动模一侧,再由推出机构将塑件从动模上推出。
(3)分型面的选择应有利于塑件的精度要求,比如同心度、同轴度、平行度等。因而,希望在模具的制造过程中尽可能地控制位置精度,使合模时的错位尽可能小。如图2-4所示的模具,A-A分型面满足把型腔放在模具同一侧时,双联齿轮的同轴度要求。

图2-4 满足同轴度的分型面
(4)分型面的选择应满足塑件的外观质量要求,如图2-5所示。

图2-5 分型面在圆弧顶端
(5)分型面的选择应有利于排气。在分型面上与浇口相对的位置处可以开排气槽,以排除型腔中以及熔体在成型过程中释放出来的气体,如图2-6所示。这些气体在成型过程中若不能及时排出,将会返回到熔体中,冷却后在塑件内部形成气泡,出现疏松等缺陷,从而影响塑件的机械性能,给产品带来质量问题。

图2-6 利于排气的分型面
(6)分型面的选择应尽量使成型零件便于加工。这一点是针对模具零件的加工问题提出来的。在选择分型面时我们必须要考虑模具零件的制作加工方面的问题,尽可能使模具的成型零件在加工制作过程中既方便又可靠,如图2-7所示,左边斜分型面的型腔部分比右边平直分型面的型腔更容易加工。

图2-7 合理的斜分型面
(7)分型面的选择应有利于侧向分型与抽芯。这一点是针对产品零件有侧孔和侧凹的情况提出来的。侧向滑块型芯应当放在动模一侧,这样模具结构会比较简单,如图2-8所示。

图2-8 侧向抽芯位置
(8)分型面的选择应尽量减少塑件在分型面上的投影面积,如图2-9所示的右图中投影面积较小。
图2-9 减少投影面积的分型面
(9)分型面的选择应尽可能减少由于脱模斜度造成塑件的大小端尺寸的差异。
3.模具分型原则
一般来说,模具都由两大部分组成,即动模和定模(或者公模和母模),分型面是指两者在闭合状态时能接触的部分,也是将工件或模具零件分割成模具体积块的分割面,具有更广泛的意义。
分型面的设计直接影响着产品质量、模具结构和操作的难易程度,是模具设计成败的关键因素之一。
确定分型面时应遵循以下原则。
(1)应使模具结构尽量简单。如避免或减少侧向分型,采用异型分型面减少动、定模的修配以降低加工难度等。
(2)有利于塑件的顺利脱模。如开模后尽量使塑件留在动模边以利用注塑机上的顶出机构,避免侧向长距离抽芯以减小模具尺寸等。
(3)保证产品的尺寸精度。如尽量把有尺寸精度要求的部分设在同一模块上以减小制造和装配误差等。
(4)不影响产品的外观质量。在分型面处不可避免地出现飞边,因此应避免在外观光滑面上设计分型面。
(5)保证型腔的顺利排气。如分型面尽可能与最后充填满的型腔表壁重合,以利于型腔排气。