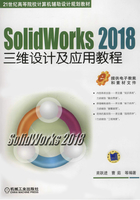
2.3 零件设计
2.3.1 零件设计基础
1. 零件建模引例
本节要建立如图2-37所示的轴承座。

图2-37 零件特征组成
(1)零件结构分析
参照该零件的加工过程,分析可知该零件包括毛坯拉伸特征、轴承孔拉伸切除特征、安装孔拉伸切除和安装孔镜像特征组成。其中毛坯拉伸特征为零件第一个特征,且应该选择图2-38中所示的草图为最佳轮廓,如图2-39所示。把模型放置在假想的“盒子”里,确定使用前视基准面为草图平面以获得最佳视角,用拉伸凸台特征形成实体。其他特征建立顺序如图2-40所示。

图2-38 最佳轮廓

图2-39 最佳草图平面

图2-40 SolidWorks的零件设计过程
(2)零件建模过程
分析零件特征组成,确定特征创建顺序,再选择特征最佳草图轮廓和草图平面后即可开始零件建模,具体步骤如下。
1)建立新零件。
单击“标准”工具栏上的“新建”按钮,弹出“新建SolidWorks文件”对话框。单击“零件”,然后单击“确定”按钮,新零件窗口出现,并以“支座”名称保存。
2)基础特征——毛坯。
●选平面:选择前视基准面作为草图平面,在“草图”工具栏中单击“草图绘制”按钮插入新草图。
●先已知——矩形:单击“矩形”,如图2-41a所示,移动鼠标捕捉圆的左侧定位点,并拖动鼠标绘制矩形。按〈Ctrl〉键,单击矩形下边线和坐标原点,添加“中点”关系。在“草图”工具栏中单击“智能尺寸”按钮
,分别标注长度、高度为120mm和15mm。
●后中间——圆:在“草图”工具栏中单击“圆”按钮,在矩形上方完成圆的绘制。按〈Ctrl〉键,单击圆心和坐标原点,添加“竖直”关系。在“草图”工具栏中单击“智能尺寸”按钮
,单击圆线和矩形下边线,标注两者距离为60mm。单击圆线,标注圆的半径为35mm,如图2-41b所示。

图2-41 毛坯草图
●再连接——直线:绘制两条竖线,并分别添加直线和圆的相切关系,如图2-41c所示。
●裁多余:单击“剪裁”实体按钮,剪裁掉草图中多余的部分,如图2-41d所示。
●造特征:在CommandManager的“特征”工具栏中单击“拉伸凸台/基体”按钮,在“拉伸”对话框中设方向1为“两侧对称”,
为30mm并单击“确定”按钮
,则完成拉伸特征建立。
●重命名:在FeatureManager设计树中,单击“拉伸1”特征,当名称高亮显示并可编辑时,输入“毛坯”作为新的特征名称。
3)切除特征——轴承孔。
●选平面:选择“毛坯前面”,单击“视向选择”,选择“正视于”
。
●绘形状:在“草图”工具栏中单击“草图绘制”按钮插入新草图,在“草图”工具栏中单击“圆”按钮
,完成圆绘制。
●定位置:按住〈Ctrl〉键,选择毛坯前面的圆弧和圆线,添加“同心”关系。
●设大小:单击“智能尺寸”按钮,将圆的直径设为40mm,然后单击“确定”按钮
。
●轴承孔:选择“插入”→“切除”→“拉伸”命令或在“特征”工具栏命令单击“拉伸切除”按钮。如图2-42所示,在“切除-拉伸”对话框中选择“完全贯穿”,单击“确定”按钮。这种类型的终止条件总是完全贯穿整个实体模型以适应深度变化。把这个特征改名为“轴承孔”。

图2-42 打轴承孔
4)切除特征——安装孔1。
●孔定位:选择底板上平面,单击“视向选择”,选择“正视于”
。如图2-43所示,单击“草图”工具栏上的“直线”按钮
,捕捉底板上平面上下两边的中点,绘制直线,在“属性”对话框中选择“作为构造线”复选框。在“草图”工具栏中单击“圆”按钮
,完成圆绘制。按住〈Ctrl〉键,选择圆心和坐标原点,添加“水平”关系约束。在“草图”工具栏中单击“智能尺寸”按钮
,单击圆线和中心线,移动鼠标超过中心线,标注对称尺寸为100mm。单击圆线,标注其直径为10mm。

图2-43 安装孔1尺寸标注
●钻通孔:选择“插入”→“切除”→“拉伸”命令或在“特征”工具栏中单击“拉伸切除”按钮。在“切除-拉伸”对话框中选择“完全贯穿”,单击“确定”按钮。把这个特征改名为“安装孔1”。
5)镜像特征——安装孔2。
选择“插入”→“阵列/镜像”→“镜像”命令。在特征树中选择“右视基准面”作为镜像平面,选“安装孔1”为要镜像的特征,单击“确定”按钮,改名为“安装孔2”。
6)编辑材料。
右击特征树上的“材料”特征,在弹出的快捷菜单中选择“编辑材料”→“黄铜”命令,完成材料的添加。
7)保存结果。
在“标准”工具栏中单击“保存”按钮,或者选择“文件”→“保存”命令来保存所做工作。
8)视图显示方式。
如图2-44所示,SolidWorks的“显示”工具栏中提供显示控制,其中“显示方式”中提供了许多实体模型在屏幕上不同的显示方式。

图2-44 显示方式和对应按钮
2. 零件建模步骤
由以上引例可见:三维零件设计过程是零件真实制造过程的虚拟仿真,其建模过程可总结为:分特征→定顺序→选视向→造基础→添其他→选材料。
1)分特征:分析零件的特征组成、相互关系及特征的最佳轮廓;如引例中的轴承座,包括毛坯、轴承孔、安装孔等特征,其中前者相关面是后两者的草图平面,而后两者均完全贯穿前者。
2)定顺序:确定特征的构造顺序、构造方法和关联方式。
3)选视向:确定基础特征的最佳草图平面和草图轮廓。基础特征是零件的第一个特征,其位置决定了零件在三维空间的位置和将来工程图中各个视图的位置。为了提高工程图生成的效率和观察模型便利,必须慎重选着其草图平面。如,引例中选择前视基准面为基础特征的草图平面时,其轴测图更美观。
4)造基础:按照确定的最佳草图平面、最佳草图轮廓和特征造型方法建立零件的第一个特征,即基础特征。
5)添其他:按照特征之间的关系,参照零件加工过程创建剩余特征,即“如何加工就如何造型”。
6)选材料:为零件选择合适的材料。
2.3.2 设计意图体现
1. 零件的设计意图
关于尺寸数值被改变后,模型会如何变化的计划称为设计意图。在参数化建模程序中尺寸参数控制着模型的结构,所以设计意图的表达就十分重要。例如,引例中零件的设计意图是:所有的孔都是通孔,安装孔是对称的,顶端孔的位置从基准面开始测量。
2. 设计意图的影响因素
开始零件建模时,选择哪一个特征作为第一个特征,选择哪个外形轮廓最好,确定了最佳的外形轮廓后,对草图平面的选择有何影响,采用何种顺序来添加其他辅助特征,这些都要受制于设计意图。为了有效地使用SolidWorks这样的参数化建模软件,建模前必须考虑好设计意图。
(1)草图对设计意图的影响
影响设计意图的草图因素包括几何约束、尺寸关系和草图的复杂程度。
●几何约束的影响。草图几何约束的影响包括草图平面的选择和图线的位置关系。如图2-45a所示,选择大圆盘上表面为小圆柱草图平面时,下面大圆盘厚度10mm变化时总高度增加,小圆柱高度30mm不变;选择大圆盘下表面为小圆柱草图平面时,下面大圆盘厚度10mm变化时总高度40mm不变,小圆柱高度减小。

图2-45 草图平面选择对设计意图影响
●尺寸关系的影响。尺寸关系某种程度上也是反映了设计人员打算如何修改尺寸。如图2-46a所示,无论矩形尺寸100mm如何变化,两个孔始终与边界保持20mm的距离。如图2-46b所示,两个孔以矩形左侧为基准进行标注,尺寸标注将使孔相对于矩形的左侧定位,孔的位置不受矩形整体宽度的影响。如图2-46c所示,标注孔与矩形边线的距离以及两个孔的中心距,这将保证两孔中心距离不变。

图2-46 尺寸约束产生的不同设计意图
●草图复杂程度的影响。很多情况下,同一零件可以由一个复杂的草图直接生成,也可以由一个简单的草图生成集体特征后,再添加倒角等附加特征来生成。如图2-47所示的零件,可以用圆角草图拉伸获得,也可以用拉伸直角草图后再添加圆角特征的方法获得。其中复杂草图拉伸法,建模速度较快,但草图复杂,不利于以后的零件修改和在装配条件下压缩圆角等细节,而简单草图拉伸法则更利于以后的修改操作。

图2-47 草图复杂程度的影响
a)复杂草图 b)简单草图
(2)特征对设计意图的影响
设计意图不仅仅受草图的影响,特征构造方法、特征构成、构造顺序及其关系等对设计意图也有很大影响。
●特征构造方法的影响。对于图2-48所示的简单台阶轴就有多种建模方法。制陶转盘法:如图2-48a所示,制陶转盘法以一个简单的旋转特征建立零件。一个单个的草图表示一个切面,其包括所有作为一个特征来完成该零件所必需的信息及尺寸。层叠蛋糕法:如图2-49b所示,层叠蛋糕方法建立这个零件,一次建立一层,后面一层加到前一层上。制造法:如图2-49c所示,首先拉伸基体大圆柱,然后通过一系列的切割来去除不需要的材料。

图2-48 简单台阶轴建模方法
a)制陶转盘法 b)层叠蛋糕法 c)制造法
以上3种方法体现了不同的设计思想。制陶转盘法强调了阶梯轴的整体性,零件的定义主要集中在草图中,设计过程简单,但草图较为复杂,不利于后期修改;层叠蛋糕法符合人们的习惯思维,层次清晰,后期修改方便,但与机械加工过程恰好相反;制造法是模仿零件加工时的方法来建模,也就是“怎样加工就怎样建模”,该方法不仅具有层叠蛋糕法的所有优点,而且在设计阶段就充分考虑了制造工艺的要求。
●特征构成的影响。选择不同的特征建立模型很大程度上反映了模型的设计意图,而且直接影响零件以后的修改方法和修改的便利性。特征建模的基本原则是根据零件的加工方式和成型方法、零件的形状特点以及零件局部细节等来选择合适的特征。如,利用传统的车削、铣削等方法完成的机加工零件不宜采用很复杂的特征;通过注塑或压铸方法成型的薄壁零件,要考虑拔模和壁厚均匀的问题;铸造零件要考虑零件出模的分型面来选择适当的草图平面,零件的出模方向则需要考虑添加适当的拔模角度,而“抽壳”特征则需要保持零件的壁厚基本均匀;钣金和焊接零件,可采用SolidWorks的钣金工具和焊接工具进行建模。
●最佳轮廓的影响。在拉伸时,最佳轮廓可比其他轮廓建立更多的模型部分。在图2-49中,分别显示了模型的3种可能轮廓和零件的最终特征组成,读者思考一下选择哪一个轮廓最好。

图2-49 “最佳”轮廓和零件特征规划
轮廓A是矩形的,比模型本身大很多,需要很多的切除或凸台来去除或添加材料以及建立一些细节,才能完成建模;轮廓B使用模型上“L”形的一条边,提供了较好的基本外形,但是需要一些额外的工作来形成半圆形的末端;轮廓C是最好的,只需再添加两个凸台,就可以完成基本外形,然后再建立切除特征和圆角特征,即可完成模型。
●观察角度的影响。在SolidWorks的模型空间里,零件的摆放位置多种多样。事实上,模型在三维空间的摆放位置与建模本身的要求没有太大的关系,合理地选择模型的观察角度是基于如下的考虑:在零件环境中,可利用视图定向工具切换到适当的角度,便于设计者观察;在装配体中,便于零件定位和选取配合对象;在工程图中,与标准投影方向一致,便于生成视图。
如将引例中的零件,在投影空间中放置几次,即可发现最佳轮廓在上视基准面上。
3. 零件建模规划
零件的造型过程,就是对组成该零件的形状特征进行造型的总和。把零件分解成若干个特征,并确定特征之间组合形式与相对位置及其构造方法的过程称为零件规划。零件规划包括特征分解、特征关联等内容。
(1)特征分解
在基于特征的零件设计系统中,特征的组成及其相互关系是系统的核心部分,直接关系着几何造型的难易程度和设计与制造信息在企业内各应用环节间交换与共享的方便程度。
零件的第一个特征为其基础特征,特征的组合形式通常有叠加和挖切。其分解原则可总结为“达意图、仿加工、便修改”。
1)特征应具有一定的设计和制造意义。如为了使减速器从动轴能够满足设计要求和工艺要求,它的结构形状形成过程和需要考虑的主要问题,如表2-7所示。
表2-7 从动轴的结构分析

2)特征应方便加工信息的输入。按照设计意图合理规划特征关系出现的层次。比较固定的关系应当封装在较低的层次,而需要经常调整的关系放在较高的层次。
3)特征应有利于提高造型效率,增加造型稳定性。应仔细分析零件,简单、合理、有效地建立相应草图;严格按机械制图原则绘制草图;合理应用尺寸驱动、几何关系,方便日后修改与零件产品系列化;圆角、倒角等图素尽量用相应的辅助特征实现,而不在草图中完成。为了观察方便和简化工程图生成时的操作,需要按照观察角度合理地选择基体特征草图平面。
按照上述原则分析,可得到图2-50所示零件的特征构成。

图2-50 零件建模前的规划过程示例
(2)特征关联
如果一个特征的建立参照了其他特征的元素,则该特征称为子特征,被参照特征称为该特征的父特征,父特征与子特征之间形成父子关系,也叫特征关联。例如,带孔板的特征组成如图2-51c所示,其父子关系如图2-51f所示。

图2-51 带孔板特征构成及其父子关系
a)拉伸特征 b)打孔特征 c)孔倒角特征 d)棱倒角特征 e)设计树 f)特征的父子关系
在特征管理树中,子特征肯定位于父特征之后。删除父特征会同时删除子特征,而删除子特征不会影响父特征。
特征关联方式有:草图约束关联、特征拓扑关联和特征时序关联等几种类型。
1)草图约束关联:指定义草图时借用父特征的平面作为草图平面,草图图线与父特征的边线建立了重合、相切等几何关联或距离、角度等尺寸关联关系。如图2-52b所示,零件建立的草图关联关系包括凹槽特征的草图平面为圆柱的上表面及其草图圆距圆柱边线10mm。
2)特征拓扑关联:拓扑关系指的是几何实体在空间中的相互位置关系,例如,孔对于实体模型的贯穿关系等。对于拉伸特征而言,拓扑关系主要体现在特征定义的终止条件中,如完全贯穿、到离指定面指定的距离等终止条件方式决定了特征之间的拓扑关系。如图2-52c所示,零件建立了凹槽特征的高度为距离圆柱特征的下表面10mm的拓扑关联。
3)特征时序关联:时序关联指的是特征建立的先后次序。建立多个特征组成的零件时,应该按照特征的重要性和尺度进行建模。先建立构成零件基本形态的主要特征和较大尺度的特征,然后再添加辅助的圆角、倒角等辅助特征。如图2-52d所示,零件建立了拉伸凸台→拉伸切除→边线倒圆角的时序关联关系。

图2-52 特征关联方式
a)示例零件 b)草图约束关联 c)特征拓扑关联 d)特征时序关联
(3)零件规划实例
下面以图2-53所示的零件为例,说明零件建模前的规划过程。

图2-53 零件建模型
1)选择合适的观察角度。如图2-54所示。对于这个模型而言,A的放置方法最佳,应该把选择的最佳轮廓草图绘制在“上视”基准面上。

图2-54 确定合适的观察角度
2)选择最佳的草图轮廓。图2-55显示了3种可能选择的轮廓,这3个轮廓都可以用来建立模型,下面分析以下3种不同轮廓的优缺点,以便确定一个最佳的草图轮廓。

图2-55 三种草图轮廓
选择轮廓“A”:建立拉伸特征时有两种情况:拉伸的深度较短时(后面凸台的厚度),形成一个比较薄的实体,无法反映零件的整体面貌;拉伸的深度较长时(大于整个模型),将需要一系列其他切除特征切除多余的部分。
选择轮廓“B”:轮廓的整体外形是一个“L”形,这个形状可以反映零件的整体外貌。但是,拉伸特征无法形成前面的圆弧面,还需要一个圆角或切除特征来实现。
选择轮廓“C”:使用此轮廓建立拉伸时,给定一个较短深度(下部的厚度),圆弧面部分可以直接形成,再添加拉伸凸台和拉伸切除即可完成模型。因此,轮廓C是最佳的轮廓。
3)确定特征建立顺序。根据确定最佳的轮廓的分析过程划分出整个零件的建模过程,如图2-56所示。

图2-56 建模过程
4. 零件建模原则
由上述分析可见,建立零件模型绝不是“只要看起来像,怎么构建都可以”,而应该采用“怎样加工就怎样建模”的思想,建模前必须想好用怎样的特征表达零件的设计意图,必须考虑零件的加工和测量等问题。良好、合理、有效的建模习惯需要遵循以下几点原则:“草图尽量简,特征需关联,造型要仿真,别只顾眼前”。
1)草图尽量简:为了有利于草图的修改和特征的管理,草图尽可能简单,一般为“单轮廓,不倒角”,零件上的圆角和倒角用特征来生成。如图2-57所示,从单轮廓草图开始建模。

图2-57 草图尽量简
2)特征须关联:为了充分体现设计意图,提高零件的可修改性,特征之间应该有草图平面借用、特征目标参考、尺寸和几何关系约束、特征建立先后顺序等关联关系。通常,先建立构成零件基本形态的主要特征和较大尺度的特征,然后再添加辅助的圆角、倒角等辅助特征。如图2-58所示,圆筒的草图平面在平板的底面上,支管的拉伸切除终止关系为“成形到下一个面”,而不是用“给定深度”。这样通过建立与前一个特征的关联关系,不仅与其实际加工工程相似,而且再改变前一个特征尺寸时,仍然可以反映最初的设计意图,体现了“牵一发而动全身”的特点,而且提高了设计效率。

图2-58 特征须关联
3)造型要仿真:为了充分体现零件的可加工性能,减少特征分解时间,尽量参照零件的加工制造过程确定特征的组成及其建立顺序与方法。如图2-59所示,阶梯轴的建模过程参照“一夹一顶”的阶梯轴加工过程建模,而不采用旋转特征一次成形。

图2-59 造型要仿真
4)别只顾眼前:建模时,不能只考虑目前正在建模的零件建立相关特征,而应该从提高零件模型的可重复性利用程度、以后装配时减小零件规模、生成图纸和后续CAE分析等多种用途选择合理的草图和特征组成。如图2-60所示,两个零件均是由图中所示特征,圆周阵列而获得,只是角度不同而已。

图2-60 别只顾眼前