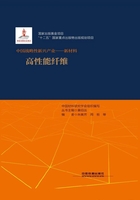
2.3 碳纤维的研究现状与发展趋势
2.3.1 PAN基碳纤维的研究现状与发展趋势
1950年Houtz等发现PAN纤维在缓和氧化的条件下,在空气中进行热处理时会变成耐燃的黑色纤维[31],首次发现PAN基碳纤维;1959年日本大阪工业试验所研究员提出PAN基碳纤维的生产技术[9];1963年英国皇家航空研究院通过在预氧化过程中施加张力成功制备出高性能碳纤维[32];1969年日本东丽公司成功研制出共聚PAN基碳纤维,并结合美国Union Carbide公司的碳化技术,成功生产出高强度、高模量的碳纤维;20世纪70年代末以来,国外许多以PAN为原料制备碳纤维的厂家展开了广泛的合作和竞争,促进了PAN基碳纤维工业的迅速发展,拓展了PAN基碳纤维的应用领域。日本东丽公司先后推出T300、T700、T800、T1000、T1100、T1200等系列碳纤维,最近又推出兼具高强度、高模量的T1100G碳纤维。目前PAN基碳纤维的生产工艺基本成熟,主要分化为以美国为代表的大丝束(48K以上)碳纤维和以日本为代表的小丝束碳纤维两大类。
为进一步提高碳纤维的力学性能,研究人员对PAN基碳纤维的每个环节进行了大量研究。在PAN纺丝原液的制备方面,Morris[33]等合成了高分子量的碳纤维前驱体PAN-co-MA,并采用干喷凝胶纺丝方法制备了高性能的前驱体纤维,断裂强度为954MPa,弹性模量为15.9GPa。Park[34]等采用纳米纤维素增强PAN纺丝原液,并使用不同浓度纳米纤维素增强的PAN为原丝生产碳纤维,发现随着纳米纤维素的加入,石墨微晶尺寸得以增加。Xiang[35]等报道了采用石墨烯纳米带制备碳纤维前驱体,所得纤维碳收率高,断裂强度为378MPa,弹性模量达到36.2GPa,拓展了碳纤维的制备方法。日本三菱人造公司在专利JP2013103992A中公布了一种含丙烯酰胺和乙烯基单体的碳纤维前驱体丙烯腈系共聚物。所得纤维的纤度为2.5dtex,长丝根数为24000,在230~260℃和260~290℃下的热值分别为470kJ/kg和850kJ/kg。在纺丝成形方面,Brown等[36]研究了凝胶纺丝中老化时间对PAN-co-MA溶液黏弹性的影响,发现当老化时间足够长时纺丝溶液中会出现不同程度的凝胶化和降解,进而影响碳纤维前驱体的结构和性能。Júnior等[37]以甘油为增塑剂采用熔融纺丝方法制备了PAN纤维,避免了有机溶剂的使用,但所得纤维力学性能较差,可纺性有待提高,不能大规模生产。在预氧化和碳化方面,Morales等[38]通过在PAN溶液中加入光引发剂,然后将湿法纺丝得到的纤维在较低温度下进行短时间的紫外光处理,有效缩短了预氧化和碳化时间。
PAN基碳纤维未来的发展主要包括两个方向。一是高性能碳纤维的制备。目前东丽公司生产的T1000碳纤维的抗拉强度为7.02GPa,即便是实验室已研制的抗拉强度为9.13GPa的碳纤维也仅达到了其理论强度的5%,因此碳纤维的抗拉强度具有很大的提升空间。碳纤维抗拉强度的提高可通过以下途径进行改进:①聚合工艺的改进;②纺丝原液纯度的提高;③PAN原丝的细旦化;④生产环境的洁净化;⑤原丝的表面处理;⑥预氧化、碳化时外场的施加。通过工艺的优化,进一步降低碳纤维表面及内部的缺陷,有望得到高强度的碳纤维。二是低成本碳纤维的开发。碳纤维由于生产成本高,目前的应用领域主要为航空航天等高端领域,在民用领域特别是汽车、建筑等行业的应用较少。有效降低碳纤维成本有利于进一步拓展其应用领域。目前降低碳纤维成本的方式主要有三种:一是原料成本的降低,包括在PAN中添加成本较低的材料,或找其他低成本碳纤维前驱体;二是成形方法的改进,采用熔融纺丝等其他低成本纺丝方法,提高纺丝速度,降低有机溶剂回收等费用;三是缩短预氧化和碳化时间,提高碳化效率。
2.3.2 黏胶基碳纤维的研究现状与发展趋势
黏胶基碳纤维是以黏胶纤维为原料,在低温热处理后再在非氧化性气氛中经800℃以上高温热处理而制得的以碳为主要成分的纤维材料[39]。黏胶基碳纤维的历史可以追溯到19世纪末,爱迪生利用棉竹等天然纤维制备成灯丝,开创了碳纤维材料的新纪元[9];1950年美国Wright-Patterson空军基地开始研制黏胶基碳纤维,通过在2000℃以上的高温将纤维进行牵伸而制得力学性能优良的纤维;1959年联合碳化物公司推出世界第一个商品化的黏胶基碳纤维Thornel-25,1964年又推出高性能黏胶基碳纤维,达到黏胶基碳纤维的鼎盛时期。此后,随着PAN基碳纤维的问世,黏胶基碳纤维行业逐渐萎缩。其原因主要包括以下三点[40]:①整体黏胶纤维工业在市场竞争中失去活力,使得其原料来源困难;②黏胶基碳纤维的生产工艺复杂,条件苛刻,碳收率低,同时对环境造成一定的污染;③黏胶基碳纤维的整体性能比PAN基碳纤维差。尽管黏胶基碳纤维较PAN基碳纤维在力学性能上不具优势,但黏胶基碳纤维独特的结构和性能决定了其固有的隔热、耐烧蚀等特性,在航空航天和军工等方面有着不可替代的用途,因此不会被完全淘汰。
黏胶基碳纤维的前驱体黏胶纤维由纤维素组成,由于分子间的氢键作用,使其裂解温度低于熔融温度,成为制备碳纤维比较理想的材料。黏胶基纤维转化为碳纤维的过程比较复杂,其过程可粗略分为四个阶段[40—42]:①第一阶段(25~150℃)主要脱掉物理吸附的水分,黏胶纤维物理吸附的水分在10%~14%之间,低温脱除掉这些水分有利于高温脱除结构水。②第二阶段(150~240℃)主要是分子结构内的脱水,生成含有羰基、酮基、烯醇基或羧基的链段(片)。③第三阶段(240~400℃)为激烈反应区,主要包括两个竞争反应,一是1,4-苷键热裂生成脱水环,1,6-键脱水生成左旋葡萄糖,并在较高温下转化为焦油;二是脱水纤维素环进一步深层次地脱水生成脱水纤维素,环内热稳定性差的C—C键和C—O键热裂生成碳四残链。④第四阶段(400~700℃)进行碳四残键的芳构化,缩聚为六碳原子的石墨层片。当温度高于700℃时,缩聚层面迅速增大,排列逐步有序化,转化为乱层石墨结构。
相比PAN基碳纤维的制备工艺流程,黏胶基碳纤维的生产工艺增加了水洗和催化浸渍过程,生产成本增大。黏胶基碳纤维的加工技术难点主要包括:①热解过程中黏胶纤维的主链十分容易断链降解,丝束强度骤然降低,出现“零强度”点;②黏胶基纤维在热解中大部分组分从原丝上逸出,导致纤维强度和碳收率变低,且溢出物易凝聚滴落在丝束上或堵塞排气系统,妨碍生产顺利进行;③提高碳纤维强度最有效的手段是在2500℃以上的石墨化过程中施加应力,使其分子链在滑移、重排取向的同时,让气泡逸出丝条外部,从而制得较高强度的黏胶基碳纤维。但是要求同时达到含碳量95%~97%(2500℃以上纤维含碳量>99.9%),两项互相矛盾的指标难度极大。上述技术难点限制了黏胶基碳纤维的制备,因此制备高性能黏胶基碳纤维时有必要从以下几点进行改进:①提高原丝质量,减小废水收缩率;②采用稀纬带技术克服零强力点;③选用混合型催化体系提高纤维强度和碳收率;④采用空气介质中低温裂解与高纯氮气中碳化两段碳化工艺。
马恒怡等[43]采用γ-辐射接枝的方法对黏胶基碳纤维的表面进行改性,结果表明辐射接枝使纤维表面粗糙度明显增大,在一定吸收剂量范围内,黏胶基碳纤维的抗拉强度提高了约20%。李新莲等[44]系统研究了影响黏胶基碳纤维收率和性能的因素,包括原丝性能、水分含量、反应气氛、添加剂种类和含量、升温速率、牵伸工艺等,指出随着生产工艺的不断完善和优化,黏胶基碳纤维的收缩率和性能会进一步得到提高。严成等[45]制备了一种具有较高强度的大孔活性碳纤维,并讨论了其产生机理,对大孔活性碳纤维的生产具有一定指导意义。
对比PAN基碳纤维,黏胶基碳纤维具有比重小、耐烧蚀、热稳定性好、导热系数低、生物相容性好等优点,同时具有一定的韧性,便于深加工,因此在航空航天、环境净化、生物医用和超级电容器等领域具有广泛的应用。目前国内黏胶基碳纤维的研究进展缓慢,很难满足军工、民用等方面的需求,加强机理的研究,改善黏胶原丝的质量,提高黏胶基碳纤维产品的抗拉强度和耐烧蚀性成为黏胶基碳纤维未来发展急需解决的问题。
2.3.3 沥青基碳纤维的研究现状与发展趋势
沥青基碳纤维是指以沥青等富含稠环芳烃的物质为原料,通过聚合、纺丝、不熔化、碳化等工艺处理的一类碳纤维,如图2-7所示[46]。按其性能的差异又分为通用级沥青碳纤维和高性能沥青碳纤维,前者由各项同性沥青制备,又称各向同性沥青基碳纤维,后者由中间相沥青制备,故又称中间相沥青基碳纤维。1965年通用级沥青基碳纤维由日本群马大学试制成功,1970年日本吴羽实现了其工业化生产。20世纪70年代美国UCC成功开发出中间相沥青基碳纤维,80年代初将其工业化生产。80年代沥青基碳纤维达到发展的黄金阶段,90年代沥青基碳纤维经历困难时期,后来经过整合、淘汰,形成几家实力较强的生产厂家,目前全世界沥青基碳纤维年产量约3000t[46]。

图2-7 沥青基碳纤维的制备工艺过程
沥青基碳纤维产业化的难点在于纺丝沥青的调制和沥青的熔融纺丝。与传统概念的沥青不同,纺丝沥青的相对分子质量更高,软化点在260℃以上。纺丝沥青的调制一般是采用热缩聚方法,其基本原理是沥青分子在高温下裂解出自由基碎片引发缩聚反应。通用级沥青碳纤维的纺丝沥青一般采用重质芳烃化合物氧化或热缩聚调制,其在价格上具有一定的优势。中间相沥青基碳纤维的纺丝沥青要求则较高,最初的中间相沥青是采用单纯热缩聚得到的,但软化点比较高,流动性也较差,导致纺丝温度较高,制备较困难[46]。在此基础上研究人员对其进行了改进,主要归结为以下四点:①工艺参数的改进和优化,降低软化点[47,48];②组分的提纯,加速中间相沥青的形成;③加氢改性,改善流变性;④化学合成,降低灰分。
由于纺丝中间相沥青在溶剂中的溶解性较差,目前还没有发现可完全溶解的溶剂,因此仅能采用熔融纺丝。影响沥青熔纺成形的因素较多,包括加工温度、停留时间、设备设计等,沥青的纺丝温度在300℃以上,此时的沥青会发生二次裂解-缩聚反应,因此停留时间不宜过长。此外,纺丝沥青的黏度随温度变化明显,造成其加工窗口较窄。在设备设计方面,通常选用具有快速熔化和输送功能的单螺杆或双螺杆进行输送。在熔融纺丝过程中,中间相沥青的液晶结构在纺丝过程中的剪切作用下容易沿着纤维的轴向取向排列,得到碳纤维的碳原子排列更接近理想石墨的结构,而且石墨晶体尺寸较大,致使其强度较高。而通用级沥青基碳纤维的取向不高,导致得到碳纤维的力学性能较差。同PAN基碳纤维的原丝不同,沥青纤维的拉伸强度很低,导致在后续处理工艺中保持长丝非常困难,因此常采用落筐收丝法来得到沥青长丝。此外,沥青纤维在后处理过程中也无法施加牵伸,但由于沥青分子的片状结构导致其在熔纺成形程中已得到较高的取向,因此并不影响所得碳纤维的性能。在制备碳纤维过程中,沥青纤维还需经过不熔化、碳化以及石墨化等工艺。沥青的不熔化时间较长,设备投入大,有必要进一步深入研究其机理。石墨化处理可使中间相沥青基碳纤维高模量和高导率的优异性能凸显出来,石墨化温度越高,性能越好。石墨化设备的研发及机理的研究同样是个难点。此外,沥青基碳纤维的制备也需要油剂、上浆剂等辅助产品的开发。
秦显营等[49]采用熔融纺丝方法制备了沥青基碳纤维,考察了其结构与性能的关系,并对制备高性能沥青基碳纤维的主要影响因素进行了研究,提出通过优化纺丝工艺条件、选择合理的氧化、碳化路径可改善纤维结构,提高沥青基碳纤维的力学性能。穆翠红等[50]采用电化学氧化法对中间相沥青基碳纤维进行表面处理改性,并通过溶胶-凝胶法(sol-gel)在处理后的碳纤维表面分别制备了钽、锆涂层,提高了中间相沥青基碳纤维的耐高温抗氧化性能。孙进等[51]研究了中间相沥青基碳纤维预氧化及碳化过程中结构转变规律,对优化沥青基碳纤维生产工艺具有重要的指导意义。尽管进行了大量的研究工作,但连续的中间相沥青基碳纤维技术还没有研发成功,其关键是纺丝用中间相沥青的生产和连续沥青纤维工艺的开发。此外,减少不熔化和碳化时间,降低生产成本也成为未来沥青基碳纤维的发展方向。
2.3.4 木质素基碳纤维的研究现状与发展趋势
木质素是自然界中一类具有芳香族结构的天然高分子,普遍存在于维管植物中,与纤维素、半纤维素共同组成植物的主体结构,其产量仅次于纤维素,为第二大天然高分子。作为造纸黑液的副产物,木质素由于具有原料来源广、价格低廉、含碳量高(>60%)、可再生等优点而颇受关注。2007年美国橡树岭国家实验室(ORNL)指出木质素基碳纤维的价格为PAN基碳纤维的几分之一,成为未来低成本碳纤维的发展方向。木质素的结构复杂,且不同来源得到的结构相差较大,目前普遍认为木质素为具有三维网状交联结构的天然高分子[52],但也有研究者指出木质素的结构为线性结构[53,54]。木质素基碳纤维最早由日本的Otani S[55]开发,并由日本化药公司对航天级小丝束碳纤维进行了试探性半商业化生产,但所得纤维力学性能较差,性能与成本不能与其他碳纤维相竞争。随后采用熔融纺丝技术以及对木质素进行改性处理,为制备高性能木质素基碳纤维打开了通道。20世纪90年代末美国能源部(DOE)开始资助ORNL进行木质素基碳纤维的开发,旨在将其应用在汽车领域,减小汽车质量,降低能源消耗。其目标价格为11~15.40美元/kg,目标性能为断裂强度达到1.72GPa,弹性模量达到172GPa。但目前实验室所做的最好性能为断裂强度达到1.07GPa,弹性模量达到83GPa,仍未达到目标要求。其根本原因是木质素分子链在加工过程中不能很好地取向,导致其力学性能较差。
木质素在熔纺成形前一般需要对原料进行提纯,ORNL提出的要求为:①木质素含量大于99%;②碳水化合物质量分数小于0.05%;③挥发成分含量低于5%;④灰分含量小于0.1%;⑤不熔颗粒(大于1mm)含量小于0.05%。对木质素的提纯目前主要包括碱提纯和有机溶剂提取两种,其基本原理是将可溶性物质和不溶物质分开,达到纯化的目的。Brodin等[56]采用陶瓷膜和离子交换膜纯化木质素,所得灰分满足纺丝要求。Baker[57]对比了有机溶剂纯化的木质素和未处理的木质素,发现经有机溶剂纯化后木质素的可纺性大幅提高。为了得到可纺性较好地木质素,一般需对提纯后的木质素进行进一步的处理,主要包括以下几种方法:①加氢和重质化处理。木质素中存在的热不稳定的官能团及键,经加氢后被消除,转换成分子可旋转的立体结构。同时,由于木质素的分子量较低,且含有较多挥发性小分子,因此,需在加热减压下抽滤去除小分子,提高木质素的分子量。Sudo等[58]采用氢化处理方法对木质素进行热熔化改性制得熔融的黏稠性材料,通过传统的熔融纺丝法得到较好的木质素纤维。②化学改性法。木质素中含有醇羟基和酚羟基,可与酰化试剂发生酰化反应,从而改变木质素的热熔性。Uraki等[59]采用醋酸制浆法得到的有机溶剂型木质素为原材料制备碳纤维。在纺丝过程中,发现纺丝液的可纺性是由木质素的分散性和木质素在制浆时部分羟基被乙酰化作用所引起的。Kubo等[60]同样采用醋酸制浆法得到的软木木质素作为原材料,通过除去木质素中不溶的高分子分馏物和不稳定物质后,在350~370℃的温度下制得木质素纤维。③物理共混法。采用高聚物与木质素共混可有效改善木质素的脆性问题,提高可纺性。木质素与高聚物之间的相容性及相互作用对所得纤维的力学性能影响较大。相容性好的高聚物包括PEO、PET、PVC、PLA等,相容性较差的高聚物包括PP、PVA等[61-63]。Kadla等[61]通过将木质素与PEO共混,降低了木质素的玻璃化转变温度,可纺性提高,所得纤维抗拉强度为300~500MPa,弹性模量为30~60GPa。尽管PEO可有效提高木质素的可纺性,但所得原丝稳定性较差,后续加工过程中容易发生黏连,影响碳纤维的性能。Kubo等[62]对比了PET/木质素,PP/木质素的可纺性,发现PET和PP均能提高木质素的可纺性,但相容性不好的PP会导致所得的纤维呈中空或多孔状,进而影响碳纤维的力学性能。
尽管通过改性,木质素的可纺性有所提高,但所得碳纤维的力学性能却有待改善。在弹性模量方面,碳纤维的弹性模量理论上可接近石墨的理论模量1020GPa,实际生产的PAN基碳纤维弹性模量已达900GPa,接近目标模量[64]。但目前木质素基碳纤维的弹性模量则要小得多,文献报道中最好的达到94GPa,不足理论模量的1/10[62],亟需提高。针对木质素基碳纤维模量低的缺陷,可通过在加工过程中施加张力或优化热处理工艺来提高碳层状平面的轴向取向。在拉伸强度方面,木质素基碳纤维同样远远小于其他碳纤维,影响其纤维强度的因素主要包括纤维缺陷、纤维结构和纤维直径等。Uraki[59]等发现木质素纤维在碳化后,横截面上未出现类似沥青基碳纤维的放射性条纹,而是呈平行状结构,表明在纤维轴向上不具备六角形网状结构的结晶碳,从而导致其力学性能较低。Kubo[60]等发现木质素在熔纺过程中纤维表面会出现微孔,这种微孔经预氧化过程处理后仍然存在,大大降低了碳纤维的力学性能。碳纤维的抗拉强度和弹性模量一般随直径的增大而减小,目前所得木质素基碳纤维的直径较大也是导致其力学性能较差的原因。
随着汽车轻量化时代的到来和石油资源的日益短缺,开发低成本可再生碳纤维成为未来的发展方向。因此木质素基碳纤维的发展方向主要包括以下几点:①绿色低成本纯化工艺的研究。通过研究木质素的纯化工艺,降低整体的生产成本,在价格上体现绝对的优势。②木质素的增韧改性研究。将木质素进行合适的化学改性或物理共混,提高其可纺性,改善其脆性大的特点,得到优质的木质素纤维。③加工工艺的改进。采用外加场等方式缩短预氧化和碳化时间,增大结晶碳的取向排列,提高其力学性能。