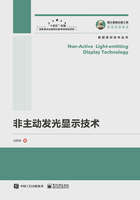
3.5.3 成盒制造技术
成盒制造技术是把TFT基板和CF基板贴合并在中间封闭液晶,制作成合格的液晶显示屏,提供给模组工程进行组装。如图3-27所示,成盒制造工艺一般分为前、中、后3个部分:前工程主要进行配向处理,中工程主要进行液晶滴下(One Drop Filling,ODF)和真空贴合,后工程主要进行切断和贴偏光片。

图3-27 成盒制造流程图
1.前工程
成盒制造的前工程是在TFT基板和CF基板表面形成一层均匀的取向膜并固化,通过摩擦或光取向处理,使其对液晶分子具有取向控制力,使液晶分子具有正确、稳定的取向,并形成一定的预倾角。前工程的主要工序有:投入洗净、取向膜印刷、取向膜烧成、摩擦、摩擦后洗净。其中,关键工艺是形成厚度均一的取向膜,进行表面均匀的取向处理。
投入前洗净的目的是除去TFT基板和CF基板上的异物粒子和污染物,提高取向膜的印刷性。常用的洗净方法如表3-1所示。洗净效果的评价项目包括有机污染物去除能力、异物粒子的去除能力、干燥性和涂布性。有机污染物去除能力的评价内容包括:EUV照度和有机膜去除性的相关评价,药液温度和洗浄能力的相关评价(CF侧),搬送速度和洗浄能力的相关评价。异物粒子的去除能力的评价内容包括:刷子的压入量和洗浄能力的相关评价,空化水射流(Cavitation Jet,CJ)压力/流量和洗浄能力的相关评价。干燥性的评价内容是气刀流量、高度、位置、角度和去水能力的相关评价。涂布性的评价内容是EUV照度和涂布性的相关评价。
表3-1 常用的洗净方法

取向膜印刷的目的是在TFT基板及CF基板上均匀地印刷一层可使液晶分子取向的取向材。所使用的取向材为聚酰亚胺(Polyimide,PI)。PI在大面积均匀性、涂覆性、摩擦性、取向控制力、化学稳定性及对液晶兼容性等方面均优于其他高分子。取向膜印刷之后进行预干燥,取向膜中溶剂成分部分挥发,烧成时基板被加热到更高温度,使溶剂全部挥发,并且取向材固化(亚胺化)形成聚酰亚胺。取向膜固化后,通过布摩擦或紫外光照射取向膜,使取向膜具有取向液晶的能力,使液晶排列具有预期的预倾角。
摩擦后洗净的目的是去除摩擦工程后基板上的异物及污染物,防止异物不良和取向不良,包括有机污染物(摩擦布)和异物粒子(摩擦布、取向膜残屑)、离子性不纯物等。在摩擦洗净工程中,为了保证取向的均一性,必须保证洗净的均一性。
2.中工程
成盒制造的中工程是在CF基板和TFT基板之间注入液晶并贴合密封。中工程的主要工序有:封框胶涂布、液晶滴下、真空贴合、封框胶硬化。其中,关键工艺是形成盒厚均一的显示屏,同时要避免液晶被污染。
涂布封框胶的目的是连接CF基板和TFT基板,防止液晶泄漏。在封框胶中混入直径在3~10μm的间隙子,有利于控制周边盒厚,有利于后工程的切断。封框胶材的黏度范围大,为20~700Pa·s。一般要求封框胶的涂布位置精度在80μm左右,涂布幅宽为0.2~0.4mm,涂布高度为25~50μm,断面积精度在10%左右。如图3-28所示的显示屏角部,是封框胶涂布重点控制的区域。为了保证角部封框胶的位置和形状,一般转角的最小R描画控制在0.5mm左右,涂布速度控制在20~100mm/s。

图3-28 显示屏角部的封框胶位置
在图3-28中,封框胶外侧设计有一小块银胶。在TFT基板的配线(一般为COM配线)上涂布银胶,使TFT基板与CF基板导通。随着封框胶内掺入导电金球工艺的成熟,银胶导电技术逐渐废弃。目前,为了对策封框胶内导电金球工艺引起的静电破坏等不良现象,也可以用含大量导电金球的金球胶代替银胶,专门涂布在封框胶外侧,使TFT基板和CF基板导通。
通过液晶滴下,在TFT基板(或CF基板)上滴下适量的液晶,形成所要求的显示屏盒厚值。液晶滴下的主要控制参数包括:液晶滴下量、液晶滴下位置、液晶滴下打点数、液晶脱泡条件(时间、真空度)和Lead Time(液晶滴下到真空贴合的间隔时间)。液晶滴下量必须适中,滴下量过多会导致周边盒厚值增大,滴下量过少会导致显示屏中央盒厚值减小。如图3-29所示,滴下位置必须适中,如果不是最佳位置,在大气开放时,将形成面内压力差,导致周边盒厚不良。

图3-29 液晶滴下位置对贴合的影响
液晶滴下之后,在真空中将TFT基板和CF基板在数微米的精度范围内进行贴合。真空贴合过程中,如果没有达到要求的真空度,贴合之后的显示屏会出现盒厚不良,产生气泡。一般要求真空度在0.13Pa以下。真空到达时间:60s内达到1Pa以下,120s内达到0.5Pa以下。在液晶脱泡不充分或排气速度太快的情况下,会导致液晶飞溅出来,若飞溅到封框胶材上,则会导致封框胶材接着不良,液晶泄漏。贴合后,通过专用的离线贴合精度测定装置,自动进行测定。一般,玻璃基板越大,贴合精度越差,G4.5生产线的贴合精度在±3μm左右,G8.5生产线的贴合精度在±7μm左右。
封框胶硬化的目的是通过UV及加热对封框胶进行充分硬化,使真空贴合后的CF及TFT基板通过封框胶高信赖性的无偏移接着,形成盒厚稳定的液晶屏。同时,防止液晶气泡的产生(长时间放置),使液晶完全扩散。封框胶硬化一般分为UV硬化和热硬化前后两个部分。UV硬化使封框胶材达到一定程度的硬化,真空贴合后的CF基板和TFT基板接着,形成稳定盒厚。热硬化使封框胶材充分硬化达到高信赖性,同时通过加热再降温使液晶各向同性(isotropic)化,进行再取向。
3.后工程
成盒制造的后工程是从贴合好的基板上切出一定大小的显示屏,并贴上偏光片。后工程的主要工序有:个片切断、研磨、洗净、显示屏洗净、偏光片贴附、显示屏检查等。
个片切断是将TFT基板和CF基板贴合后的大型基板按制品尺寸进行上下切断,分割为单块显示屏。如图3-30所示,个片切断一般先用高浸透刀片上下切断,然后分离。上下切断方式的优势是采用高浸透刀片,只划片就能使基板完全断裂,无须裂片,避免裂片时对屏产生的损伤;无大型基板翻转,避免了翻转时因夹杂异物而对屏产生损伤。

图3-30 个片切断示意图
对切出来的单个显示屏进行研磨,除去扫描线电极和数据线电极短路连接的静电破坏防止电路,使扫描线电极和数据线电极各自分离独立。通过液晶屏玻璃端面处理,防止后续工程中出现缺口及划伤驱动芯片。通过洗净和干燥处理,装入料盒进行显示屏的显示功能检查。
在偏光片贴附前,通过洗净处理除去显示屏上附着的异物。研磨头在显示屏上移动,去除异物;研磨带一般呈卷曲状态,可以防止异物再附着和磨耗;研磨使用湿处理方式,可以防止显示屏表面损伤和静电破坏。根据显示屏的液晶取向方向,将偏光片的偏光轴与之重合进行贴附。显示器和手机等中小尺寸的显示屏,一般呈水平状态进行偏光片贴附,CF侧和TFT侧的偏光片依次进行贴附。电视等大尺寸的显示屏,一般呈准垂直状态进行偏光片贴附。显示屏在准垂直状态,CF侧和TFT侧的偏光片可以同时贴附。这种方式还可以节约设备面积。偏光片贴附后,对显示屏进行加压加热处理,以除去偏光片之间的微小气泡。
偏光片贴附后,显示屏具备了基本的显示功能。这时,需要对显示屏进行如图3-31所示的缺陷检查,简称P检。外加电压信号通过P检设备的探针输入显示屏,通过输入不同的信号使显示屏显示各种检查所需的画面。比如,通过低灰阶画面可以检查亮点缺陷,通过白色画面可以检查暗点缺陷,通过独立的R、G、B画面可以检查左右像素短路缺陷。存在缺陷的显示屏需要降低处理,或者报废。为了减少偏光片不必要的消耗,可以在P检后进行偏光片贴附操作。这样,P检发现需要报废的显示屏就不进行偏光片贴附。这样的操作,需要在P检时在显示屏上下两侧配置通用的偏光片。由于上下两侧的偏光片没有与显示屏紧密贴合,将使一些与偏光片相关的细微的缺陷无法检出。

图3-31 显示屏检查示意图